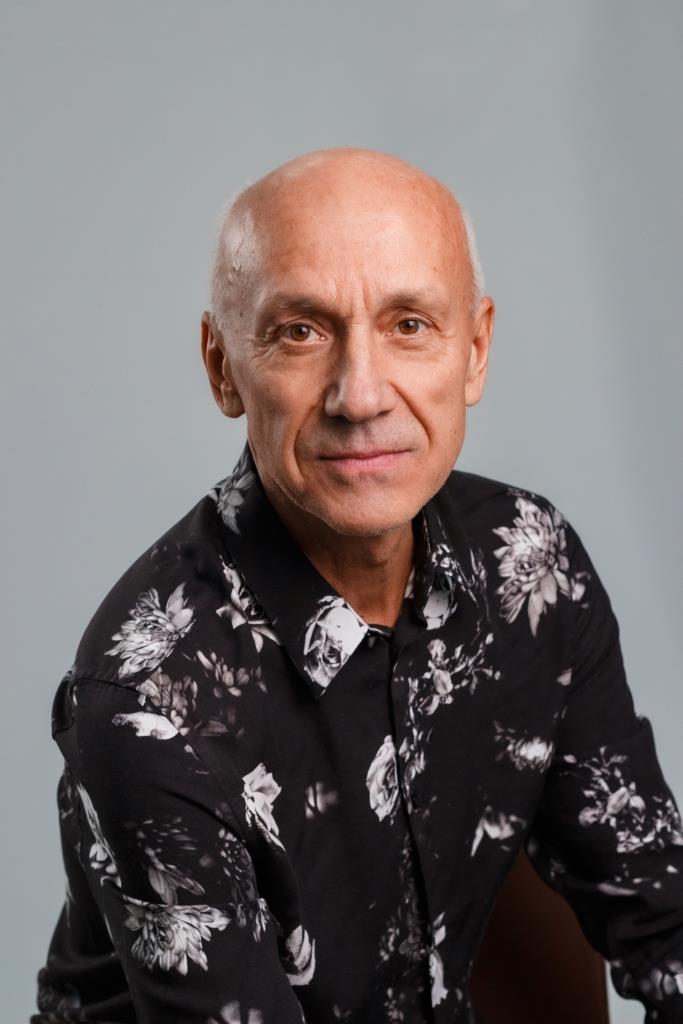
Prof. Viktor Evgenievich Kuzmichev
Technical Sciences Ivanovo State Polytechnic University, Russia
Title: CLOTHING DESIGN IN THE ERA OF ARTIFICIAL INTELLIGENCE
Abstract:
This report
addresses the challenges that have arisen in clothing design under the
influence of digital technologies and the new opportunities presented by
artificial intelligence (AI). The rapid development of digital technologies and
AI is fundamentally changing the processes of artistic and industrial clothing
design. Many functions previously performed by specialists can now be carried
out automatically. However, the formalization of professional experience and
its translation into knowledge bases, rules, and algorithms—i.e., into the
digital environment—remains a serious problem. AI technologies (such as Grok3,
DeepSeek, ChatGPT, and others) significantly reduce the scope of
three-dimensional modeling software (like Clo3D, Style3D, and others). These emerging
perspectives call for a revision of certain principles.
Among the
main challenges faced by the digitalization of design and production processes,
the following can be highlighted:
1. Generation of digital twins of textile
materials. The deformation of textile materials is considered primarily under
the influence of gravitational forces or short-term loads. Currently, the
generation of virtual twins of textile materials is based mainly on physical
and mechanical property indicators (following the KAWABATA method) and
drapability. Mathematical models used to predict the shape of three-dimensional
clothing rely on tests of flat textile material samples, leading to
inconsistencies in predicting material behavior in the three-dimensional
environment. Expanding the range of properties included in mathematical models
and bringing testing methods closer to real conditions is a crucial direction
in digital textile materials science. Equally important are results of sensory
analysis, which enable the assessment of clothing comfort.
2. Generation of digital twins of human bodies.
This issue is particularly relevant for bodies that must meet national
standards for clothing design. Typically, the number of measurement parameters
in such standards worldwide does not exceed 35-40 measurements, which is
insufficient for creating a virtual twin. In addition to linear measurements,
horizontal and vertical cross-sections and projection parameters are required
to describe the front, side, and back contours. Currently, there is no
comprehensive anthropometric database to generate virtual twins across the full
size range of bodies — from the smallest to the largest. The accuracy of
virtual twin generation in three-dimensional modeling software is limited by
the number of adjustable parameters (not exceeding 18), whereas AI-based
generation achieves an accuracy of 87% (Stable Diffusion AI) to 95% (Fusion
Brain AI). The accuracy of virtual human bodies twins significantly affects the
results of virtual clothing simulation, especially for specialized clothing
(therapeutic, medical, sports, and cosmetic). Expanding the anthropometric
database is a critical factor in fully leveraging the benefits of digital
technologies and AI.
3. Generation of digital twins of
clothing. The quality of virtual clothing generation directly depends on
reproducing the structural features of pattern details, connection methods, and
the type and number of materials used, including structural elements (linings,
reinforcements). Existing 3D visualization software (Clo3D, Style3D, and
others) delivers good results for single-layer clothing (dresses, skirts,
blouses, shirts, trousers, etc.), but the accuracy of rendered clothing
decreases as the number of materials increases. Improving the accuracy of generating
different types of clothing, characterized by their fit and three-dimensional
shape, depends directly on the thorough formalization of the internal content
of the pattern design process: the interrelationship of structural parameters,
the configuration of design lines, and understanding their influence on
clothing shape.
4. Lack of algorithms for preliminary
evaluation of design decisions, not only regarding the external appearance of
clothing but also the economic efficiency and manufacturability of industrial
production. Such algorithms, connecting different stages of design and
production, could serve as a strong barrier against economically unfeasible and
unjustified decisions.
5. Absence of universally accepted
quality assessment criteria for virtual clothing, including fit on the avatar,
proportionality, and appearance. Currently, clothing quality and appearance are
determined by the manufacturer based on the target consumer category, but this
aspect is not reflected in existing processes and technologies. It is evident
that quality improvement is directly linked to the number of design,
production, and inspection procedures performed. Developing appropriate quality
criteria, mostly expressed verbally at present, is necessary to optimize design
decision-making.
6. The generation of AI-driven images has
necessitated the restoration of a complete chain for presenting figures,
clothing, and "figure-clothing" systems in the sequence: 2D (CAD) –
2.5D (AI) – 3D (three-dimensional modeling). 2.5D images combine three views:
front, side, and back. The accuracy of such clothing images, with the
underlying figure hidden, depends on air gaps between the figure and the
clothing, clothing structure, material shaping properties, and other factors.
The parameters of 2.5D images are essential for writing prompts containing
verbal terms and numerical parameters and for generating images using AI.
The opportunities provided by AI are
still not fully evident but are vast. Firstly, the ability to parametrically
generate images (of clothing, figures, and patterns) is essential for
integrating results with existing databases and CAD systems. Secondly, using
multiple AI tools allows specialists—designers and constructors—to make
informed decisions with input from various sources, which is especially
important when addressing ambiguous issues. Thirdly, integrating AI with
existing CAD systems will enable multiple scenarios, including simulating
generative thinking and writing algorithms for the rational application of CAD
commands.
Thus,
the further development of AI technologies and their integration into clothing
modeling and design processes open new horizons for the fashion industry.
Addressing the identified challenges and actively implementing AI will
significantly enhance the quality of designed products, optimize production
processes, and meet the growing demand for personalized and comfortable
clothing.
Biography:
Professor Viktor Evgenievich Kuzmichev is a Doctor of Technical Sciences, and the Head of Clothing Design Department at Ivanovo State Polytechnic University. Graduated from Ivanovo Textile Institute (1978). Get PhD in Central Science Research Institute of Sewing Industry (1982, Moscow), Dr.Sc. in Ivanovo State Textile Academy (1995).
His professional activities encompass theoretical research and practical application of modern clothing design methods, virtual design and modeling of apparel constructions. He is the founder of the scientific school "Innovative Technologies for the Analysis and Design of Real and Virtual 'Figure-Clothing' Systems" and actively participates in international scientific cooperation by holding professorial positions at foreign universities (Wuhan Textile University, the University of Upper Alsace, France). Supervisor of 25 PhD students.
He has been honored with several awards, such as of Honored Worker of Higher Education of the Russian Federation, the Order of Friendship of the PRC. His extensive publication includes 600 scientific articles, 15 teaching-methodological books, 85 patents, and 7 monographs. In 2024, he received the Russian Federation Government Prize in Science and Technology for developing innovative technological solutions that enable the creation of multifunctional textile materials and garments.